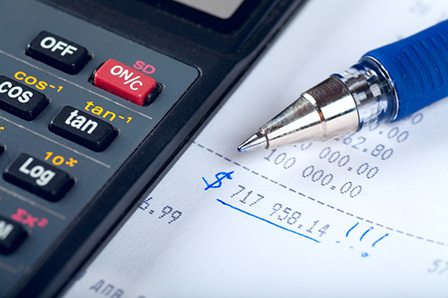
Reducing your acquisition costs
By definition, the “Total Cost of Acquisition” (TCA) is a managerial accounting concept that includes all the costs associated with buying goods, services, or assets.
Generally, it is the net price, plus all other costs needed to purchase the item and get it to the point of use.
In order to reduce total acquisition costs, it is necessary to consider and analyze not just the basic product cost, but also your entire order process costs. At GFI we take on many of the responsibilities that normally fall to the in-house staff of the end user. Working with GFI therefore allows clients to share some of their workload, and enjoy the considerable financial savings provided via the process of order consolidation. Any proficient supply chain specialist must consider their total costs of acquisition when evaluating quotations and placing subsequent orders.
List of acquisition costs normally incurred when end users directly purchase products and spares:
- Engineers time to gather information from prospective manufacturers and select the best option for the application. Communication costs for the engineer to interface with manufacturers or other suppliers.
- Purchasing staff time to place the purchase order with the chosen supplier, and associated communication costs.
- Expediting staff time used to expedite the purchase order, and associated communication costs.
- Payment costs. When buying from multiple vendors, buyers may be forced to make advance payments. Regardless of this, with a multiple vendor strategy, individual bank charges will be incurred for each order.
- Currency risk costs. When sourcing from overseas vendors, buyers can be open to the risk of currency fluctuations for long periods of time if suppliers do not quote in their preferred currency.
- Logistics staff time. When dealing directly with multiple overseas vendors, end users have to organise and co-ordinate international shipments, and incur the associated communication costs.
- Packing costs. Individual packing is inevitably required for each purchase order when using a multiple vendor strategy.
- International shipping costs. When using multiple vendors, each purchase order will incur individual shipping costs. When shipping, the greater the weight shipped, the lower the cost per kilo.
- Transit insurance costs. When using multiple vendors, buyers pay individual insurance costs on a per order basis. This costs time and money.
- Import costs. When placing multiple orders with multiple vendors, buyers incur individual import costs for each purchase order.
- Local delivery costs. When placing orders separately with multiple vendors, buyers are subject to individual local delivery costs.
- Accounts payable staff time. The more vendors you use, the more time it takes to process and instigate payments.
- Accounts payable bank charges. Obviously the greater the number of vendors used, the greater the number of payment transactions. This means higher Bank charges.